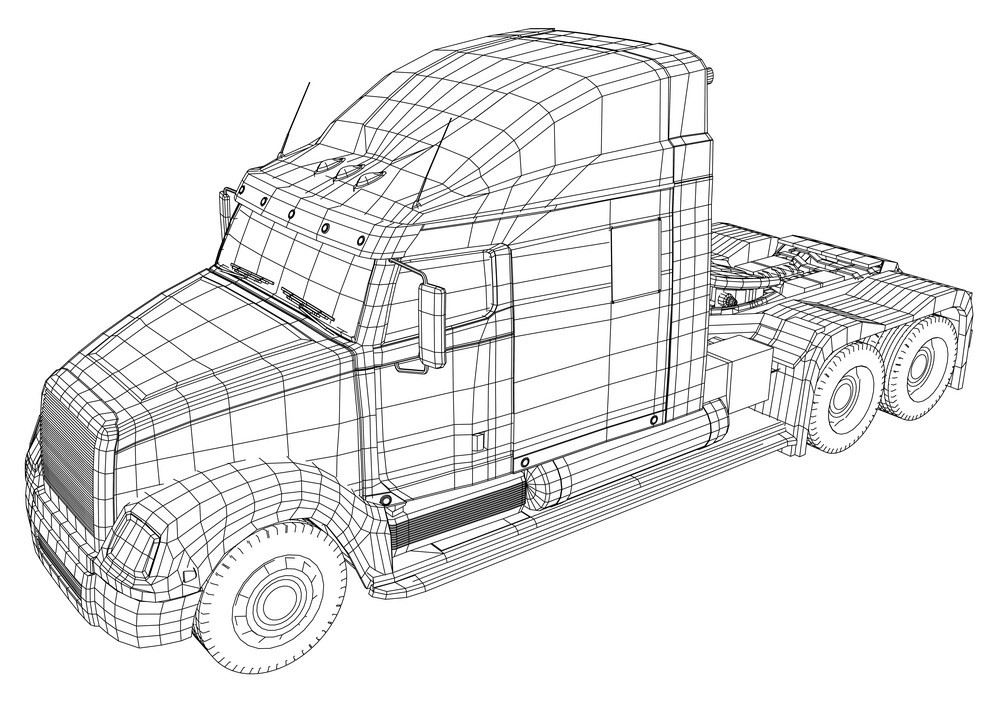
The article below was contributed c/o Chevron Lubricants.
The Importance of Choosing the Right Grease
Proper grease application in heavy-duty vehicle components is an essential part of fleet maintenance. Trucks carry heavy loads at high speeds in a wide variety of environmental conditions. It’s important to use greases that can withstand the punishment of extreme temperatures, dust and grit. That said, there is no single grease that is right for every application. In choosing grease products, it is best to match grease characteristics with performance requirements.
What to Look for:
A key characteristic to look for is the thickener, which is generally lithium or a lithium complex. The thickening agent will determine how well the grease holds up under pressure and lubricates components consistently. When re-greasing, the thickener used in the new grease should be the same as in the grease you have been using.
Another characteristic to look at is the viscosity of the oil within the grease, which actually performs the lubrication. Heavy duty trucking applications, such as axles and bearings, normally use a viscosity of ISO VG 220.
To ensure good wear protection, look for extreme pressure additives, usually denoted by an EP on the label. Most vehicle applications use EP greases. If you’re distributing grease from a centralized greasing system, you’ll want to be sure you have low-temperature pumpability to ensure the grease flows effectively to where it is needed. A high dropping point (the temperature at which a grease liquefies and stops performing as needed) is important when traveling in mountainous terrain with a lot of heavy braking and high temperatures. Water resistance is also important to reduce the risk of wash-out in wet conditions.
The Common Pitfalls to Avoid:
Do not use a moly grease in rolling element bearings, specifically wheel bearings, or slack adjusters. It can cause failure. If you use an automatic lubrication system, check to see if it has special requirements or limitations. For instance, many auto lubers do not allow the use of “tackifier” additives that increase tackiness to reduce the risk of dripping.
In our experience with customers, it pays to have an organization system in your shop to help match greases to applications. One common method is by color. Bear in mind the color of a grease serves no purpose other than to distinguish a grease from others within the supplier’s product line – and different suppliers will use different color schemes. As long as you’re getting your greases from the same supplier, you can rely on the color for identification.
Optimized greases for specific applications on the rigs can extend re-grease intervals. However, most fleets find it useful to limit the number of greases in their inventory to reduce complexity and to prevent misapplication. Many fleets have consolidated to as few as one or two greases, with a third if they use a semi-fluid grease in trailer axles. We’re also seeing a trend toward synthetic greases, which have a performance advantage in extreme temperatures.
Last, but Not Least:
Finally, good storage and handling practices matter, too. Water, dirt or particles entering a grease in an open drum can lead to wear in the components.
Grease doesn’t always get the attention it deserves compared to engine oils, for example. But it should not be overlooked as a contributor to vehicle performance and service life. If you want to be sure you’re using the right greases and getting the best value from them, just ask us.
In choosing which grease to use for commercial trucks and fleet maintenance, we hope this article was helpful.